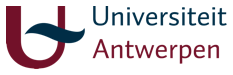
University of Antwerp
Open information exchange for flexible manufacturing
University of Antwerp: IMA Project
The Electromechanics (EM) research group linked to the University of Antwerp (formerly Artesis Hogeschool) has a long tradition in supporting manufacturing companies in the field of industrial automation. In 2012 the “Information Modelling in Automation” (IMA) project was started. This project (TETRA 110131) is funded by The Flemish Agency for Innovation by Science and Technology (IWT). The IMA consortium is made up of 12 companies and 5 research and technology organizations.
Production systems development
IMA aims to develop a methodology to exchange data, relevant to production in different types of industries, in a structured way. In some cases industrial standards are available like ISA-88 for batch control or ISA-95 for enterprise integration of control systems. However, the ‘modelling rules’ - how the data is structured and represented - specified by these standards are not always specific enough to guarantee cross-vendor interoperability. We model relevant parts of these standards using the modelling rules of OPC UA.
Many IMA consortium members are active in the fields of designing, developing and integrating flexible automation systems. Flexible automation systems allow producing small lot sizes of customized products with existing equipment. OPC UA and information modelling are valuable enablers in this domain.
One particular standard that we are mapping to OPC UA and defining an open standardized interface for is ISA- 88. ISA-88 systems with a standardized OPC UA interface have many advantages:
- Ability to choose best-value components
- Easier to reconfigure
- Easier integration
- Reduced production start-up time
These advantages translate into reduced expenses for hardware, software and component configuration as well as reduced new product start-up costs.
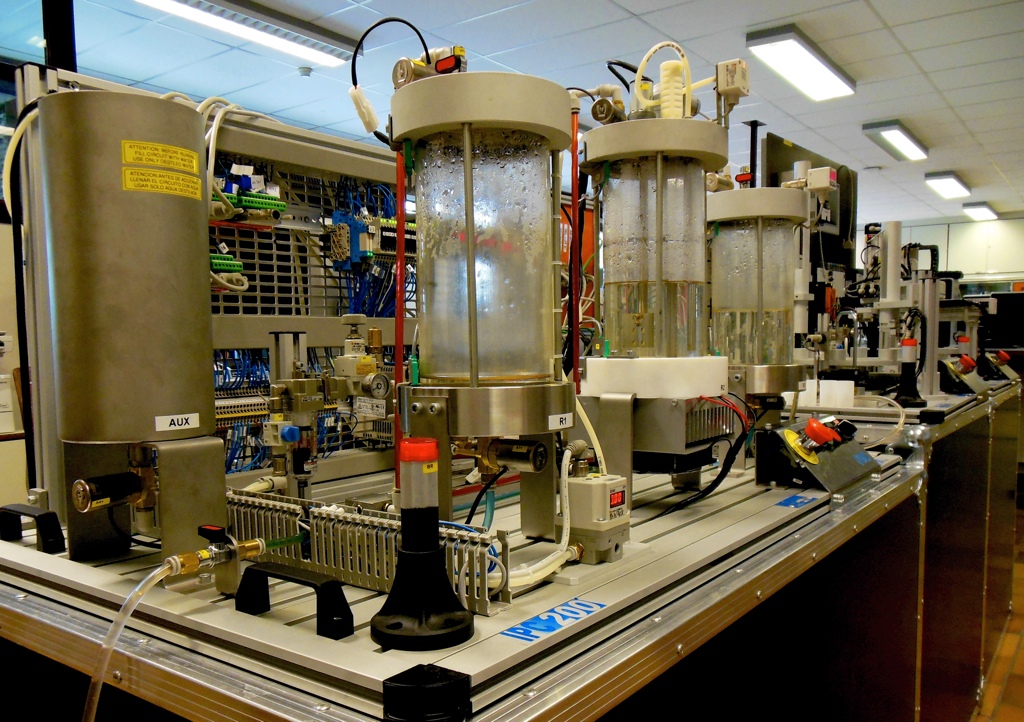
Flexible Automation System
At the University’s EM test lab our research team has created a flexible automation proof-of-concept. The setup is a lab-scale version of a soft drink production plant (SMC IPC200). This plant consists out of 3 work centres: A production station that allows batches of liquid to be mixed, agitated, heated, cooled and transferred, a bottling station, and a palletizing station. Each of the work centres is controlled by a dedicated PLC. The PLCs are from different manufacturers highlighting the vendor-independent nature of open interface flexible automation systems.
The PLCs used in this setup all have an embedded OPC UA server with a common ISA-88 based OPC UA interface developed during the IMA project. In the PLC elementary “phases” are implemented (e.g. make tank 1 ready to transfer out material). The Production Execution System (PES) contains higher-level “procedures” that coordinate these phases (e.g. transfer 1 litre of material from tank 1 to tank 2). These procedures can be assembled into a recipe, which is executed by the PES. Two alternative recipe designers were developed for the proof-of-concept.
The test setup was successfully demonstrated at the OPC Europe Day 2013 in Amersfoort. The soft drink plant can be easily reconfigured to produce new products. The Prosys OPC UA Client SDK is used in the Easy95 and Android based recipe designers. The PES uses the Prosys OPC UA Server SDK as well as the client SDK.
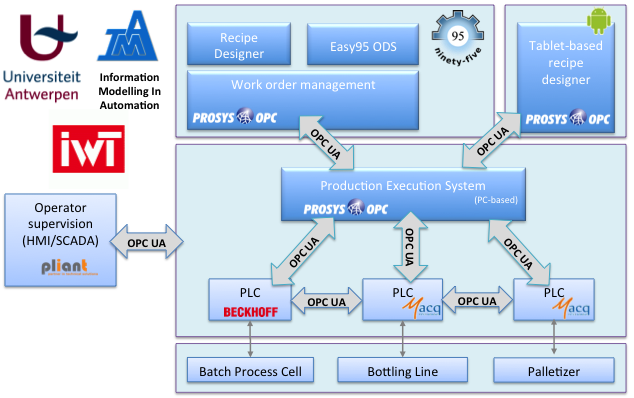
The Prosys OPC UA SDK for Java delivers a professional grade versatile toolkit for OPC UA that has been a great match for our research requirements. The Prosys SDK supports advanced OPC UA features like updating the model of the UA server during runtime. Useful examples and high quality support are provided by Prosys. We are running OPC UA on several platforms, so the true cross-platform nature of the toolkit has been very valuable.
Maarten Reekmans
Scientific Researcher: University of Antwerp
R&D Service Provider: SmarT&R
What is OPC?
OPC and OPC UA (Unified Architecture) are industry standards that enable software to connect devices, machines and systems from different manufacturers using same interface.